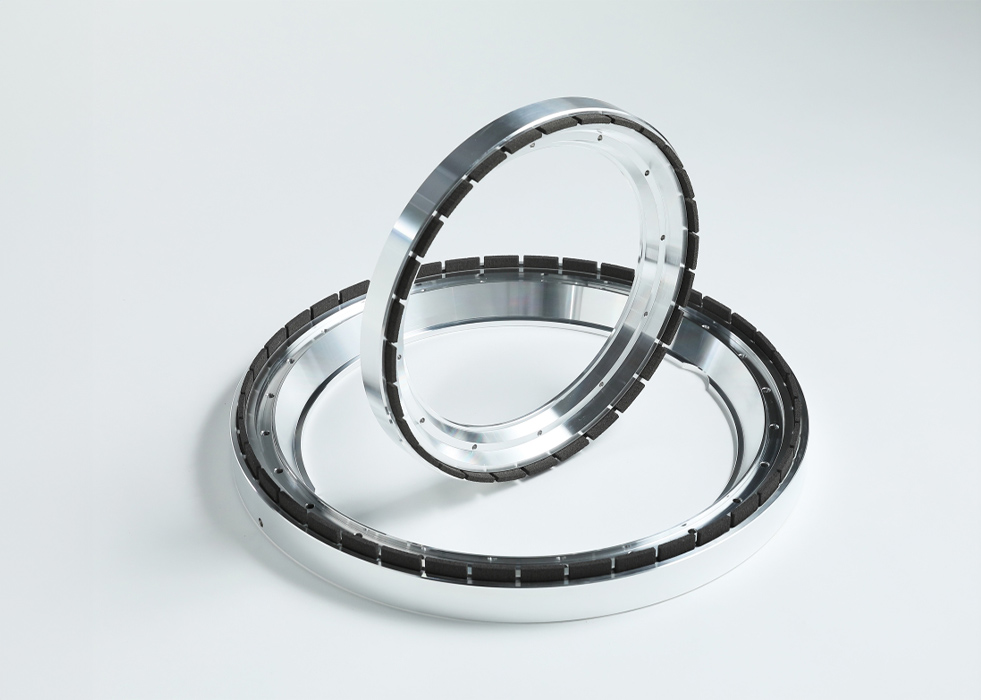
SiC面研削用ダイヤモンドホイール「M-cloud」
SiC、GaNを始めとするウェーハ面研削用メタルボンドホイールです。超多孔質構造により、これまでのメタルボンドホイールでは適用できなかった細かな粒度の研削を実現し、同じ粒度のビトリファイドボンドホイールと比較して切れ味と耐摩耗性に優れています。
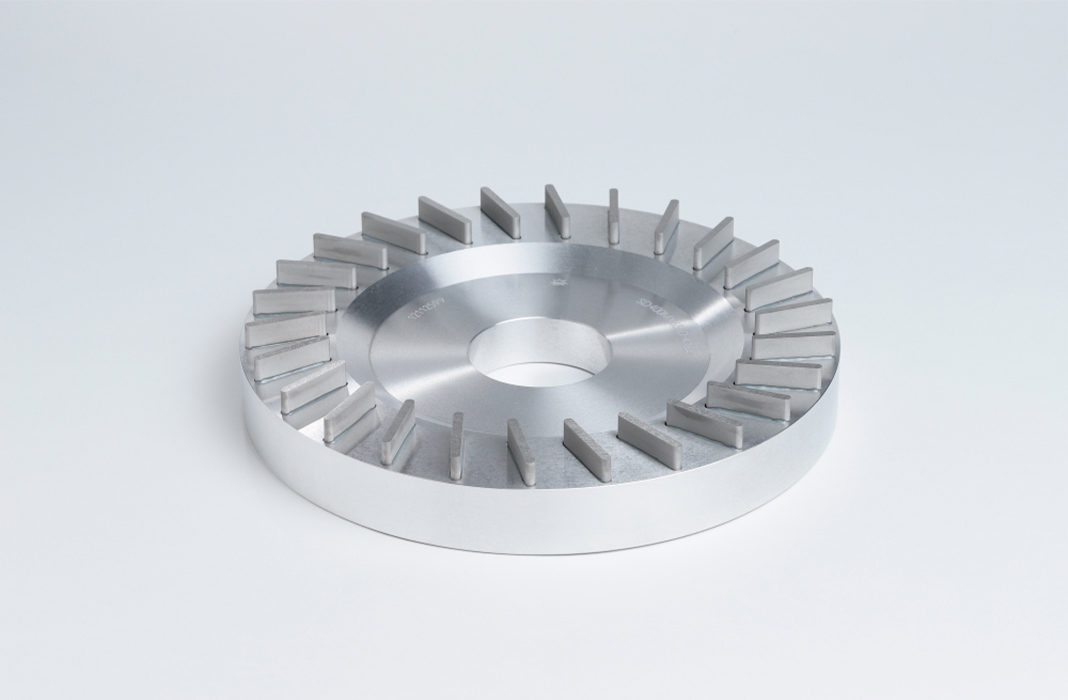
難削材対応 高能率メタルボンド「サンクレア」
サンクレアは、サファイア、超硬、セラミックス等の硬脆材料やフェライト、ネオジム鉄等の硬磁性材料、焼結部品等の鉄系材料において、従来のメタルボンドでは得られなかった領域の切れ味と寿命を実現し、加工能率の向上とコストの削減に寄与します。
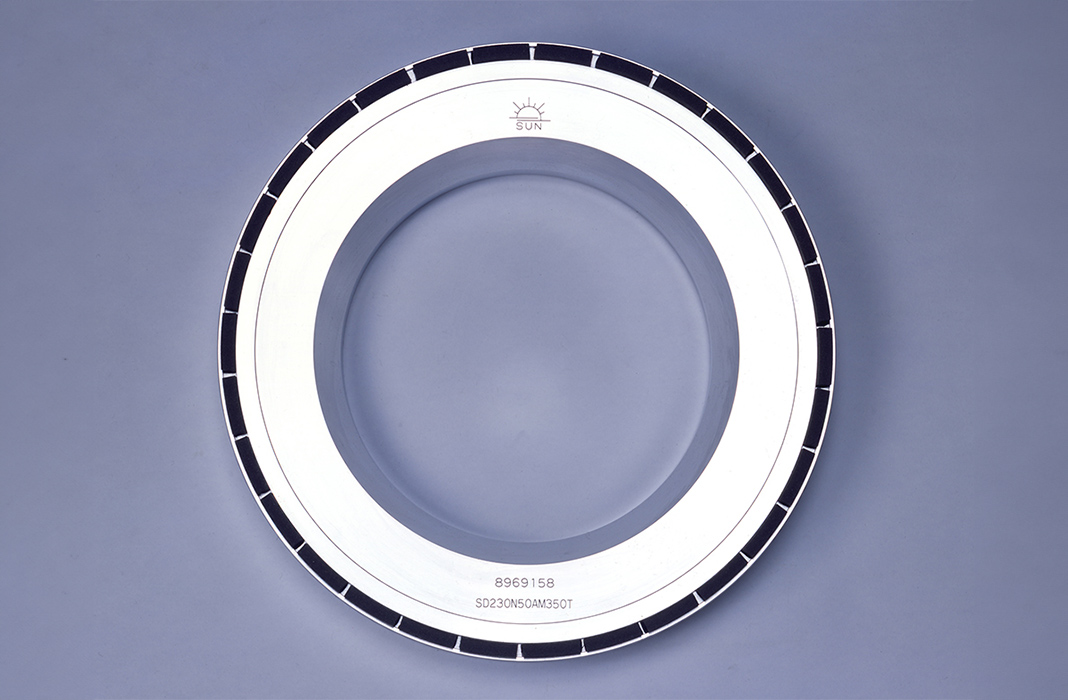
有気孔メタルホイール「エアロメタル」
特長
①切粉の排出性が良好
②安定した研削性を持つ
③耐摩耗性に優れ、長寿命
④電着ツルーアでのツルーイングが可能(CBNに限る)
①切粉の排出性が良好
②安定した研削性を持つ
③耐摩耗性に優れ、長寿命
④電着ツルーアでのツルーイングが可能(CBNに限る)
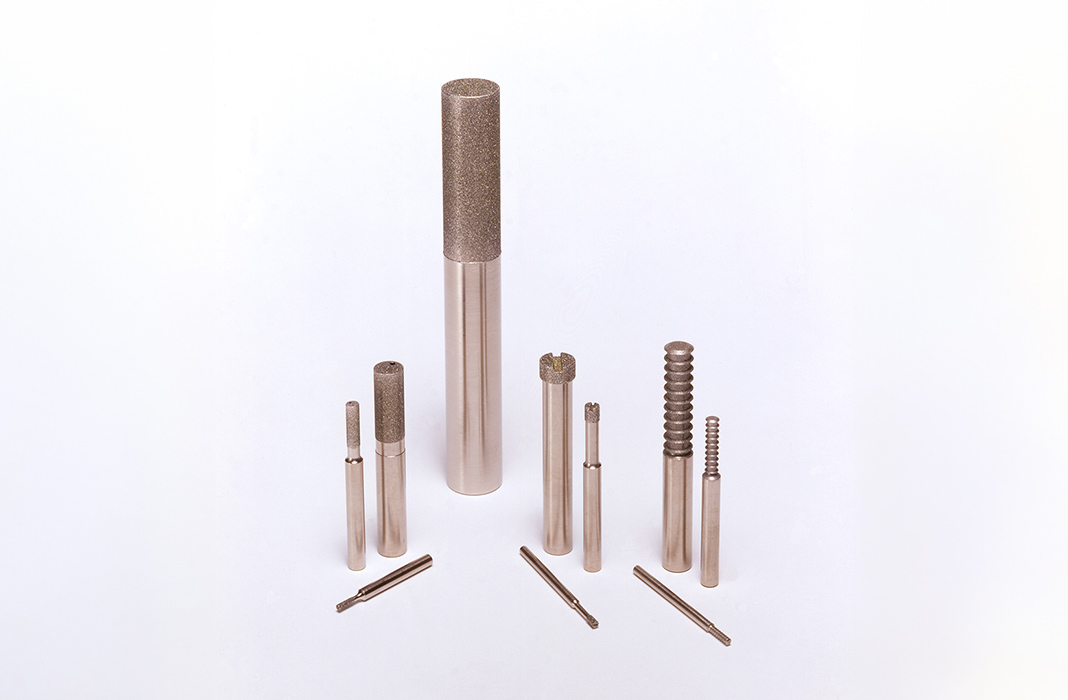
電着ホイール「セラメイトシリーズ」
半導体製造装置部品などで使用されるセラミックス加工に特化した、高精度、高能率、長寿命で安定した切れ味を発揮する電着軸付きホイール。冷却効果が高く、画期的な加工速度で高能率加工を実現したセンタースルータイプ専用のセラメイトドリル、溝加工ツールのセラメイトエンドミル、JIS2級精度(M3〜M12)のネジ加工が可能でネジ山数を半分にし、工具負荷を軽減したネジ切り加工ツールのセラメイトタップ、高速送り加工が可能な高能率コンタリング加工ツールのセラメイトコンタリング。

CMPコンディショナ
半導体デバイスやウェーハの製造プロセスにおいては、配線の微細化・多層化に伴い平坦化への要求が年々高まっています。平坦化技術として利用されているCMPプロセスにおいて、研磨パッドのコンディショニングは研磨特性を安定化する重要な役割を担っており、当社では25年以上にわたり高品質・高信頼性のコンディショナを通じてCMPプロセスの安定化に寄与し続けるともに、多様化するニーズに対応した様々な形状・仕様のコンディショナを提供しています。
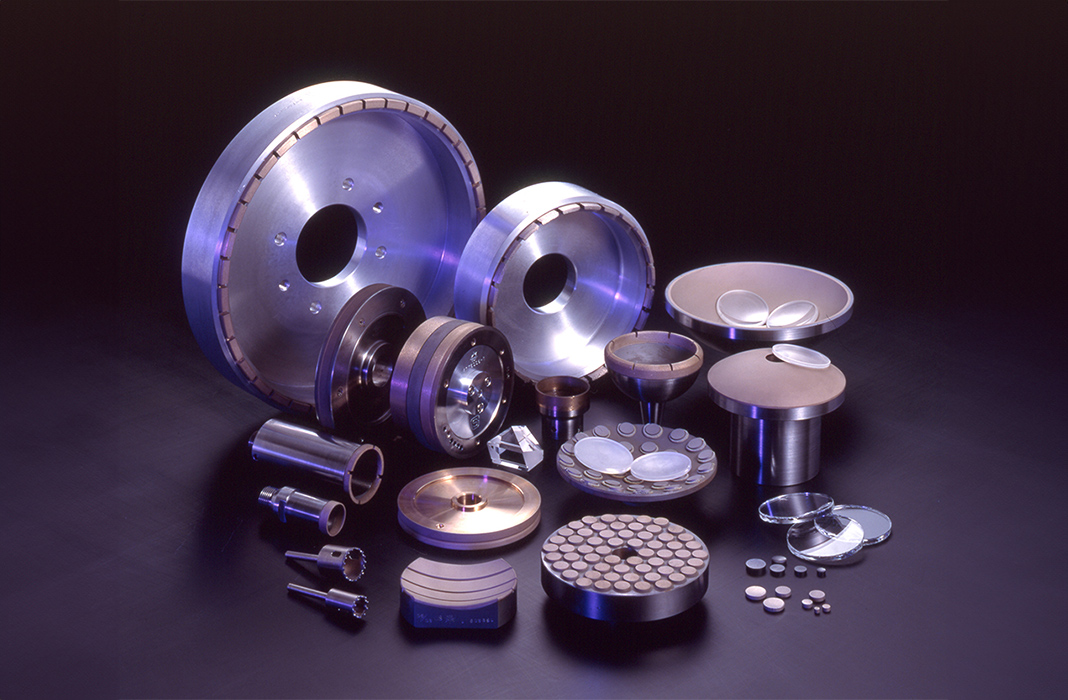
ダイヤモンドホイール(光学用ガラス精密研削用)
カメラ・双眼鏡用レンズ、プリズムそして近年ではハードディスク用ガラス基板などの加工に際して、ダイヤモンドホイールは必要不可欠な工具です。加工目的により、ペレット、カーブジェネレータ、芯取り・面取りホイールなどがあります。更に、これらはメタル、レジン、ポリックス、電着などボンドの種類によってそれぞれ高い性能を引き出しています。
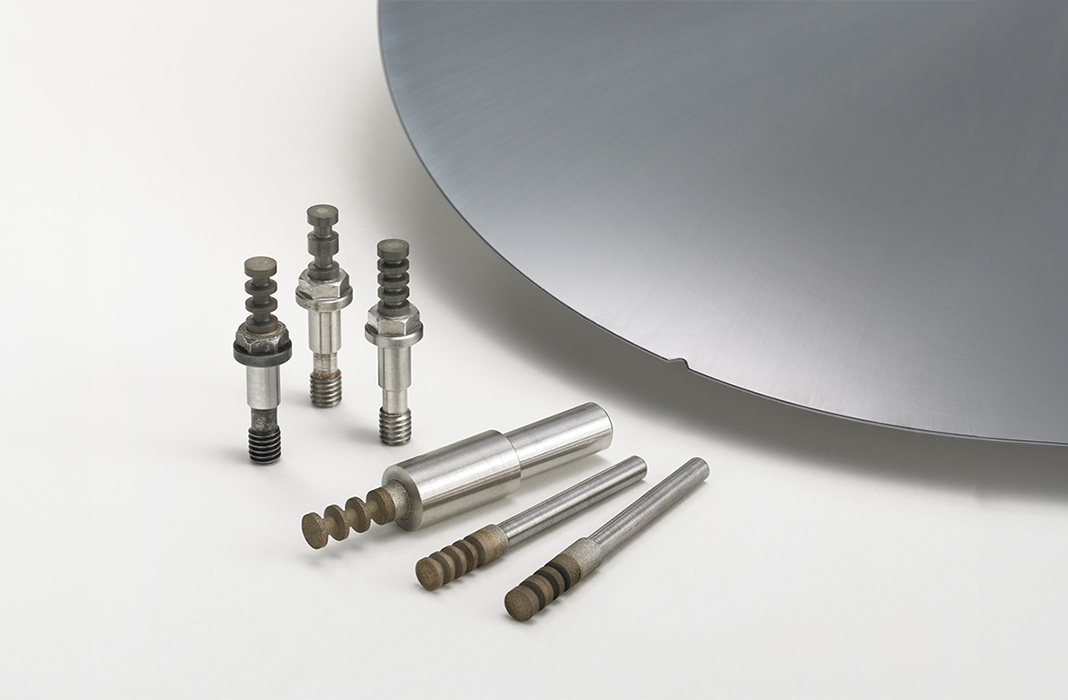
ノッチ用面取りホイール
大口径ウェーハのノッチ部仕上げ加工には小径の総形ホイールが使用されます。シャンクに対するダイヤ部の振れ精度を維持し、良好なウェーハ外周を実現します。外周用面取りホイール同様、単溝や多溝タイプ、粗・仕上げ一体型ホイール等、幅広い仕様に対応致します。
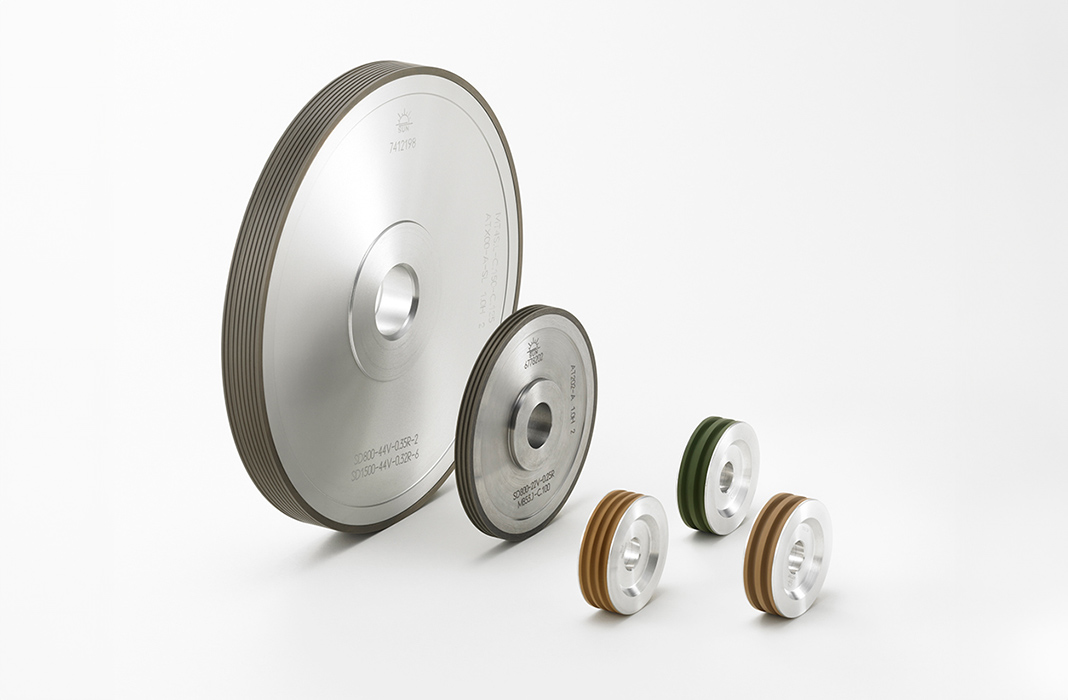
半導体ウェーハ面取り用ダイヤモンドホイール
厳しい形状精度と耐摩耗性に加え、安定した切れ味が要求されるウェーハ外周部の面取り加工には、メタルボンドホイールやレジンボンドホイールが使用されます。単溝や多溝タイプ、粗・仕上げ一体型ホイール等、幅広い仕様に対応致します。
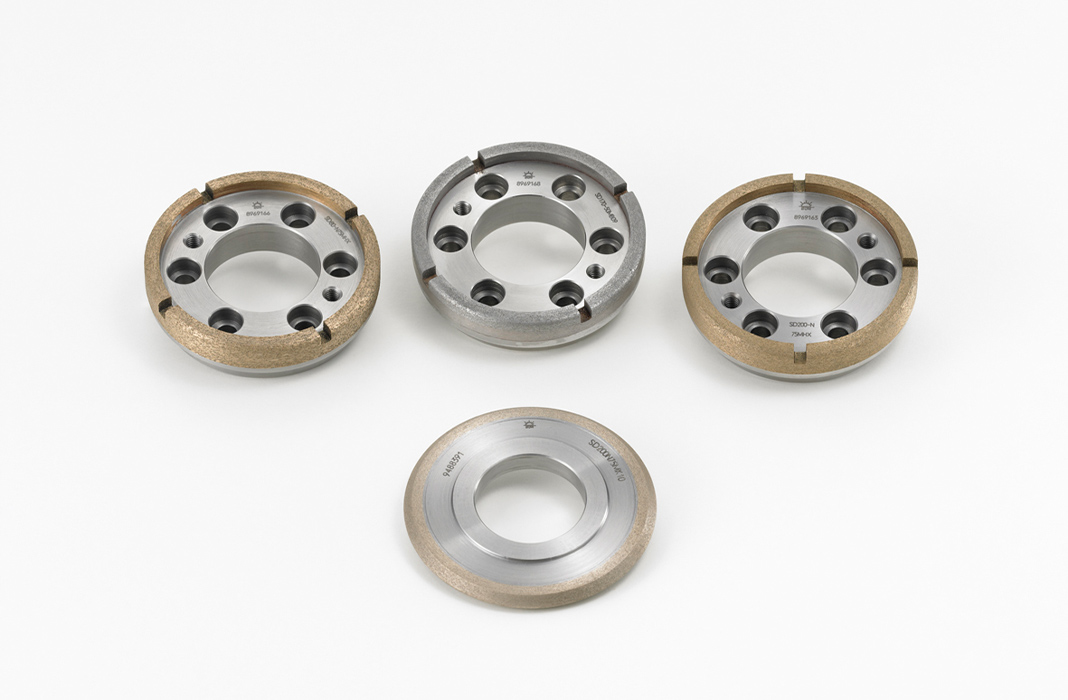
外周研削・OF用ダイヤモンドホイール
太陽電池用及び半導体用シリコンインゴットの研削加工に、ダイヤモンドメタルホイールおよびダイヤモンドレジンホイールが使用されます。様々な分野で培われた実績をもとに、お客様のニーズや保有マシンにあったホイールをご提供します。
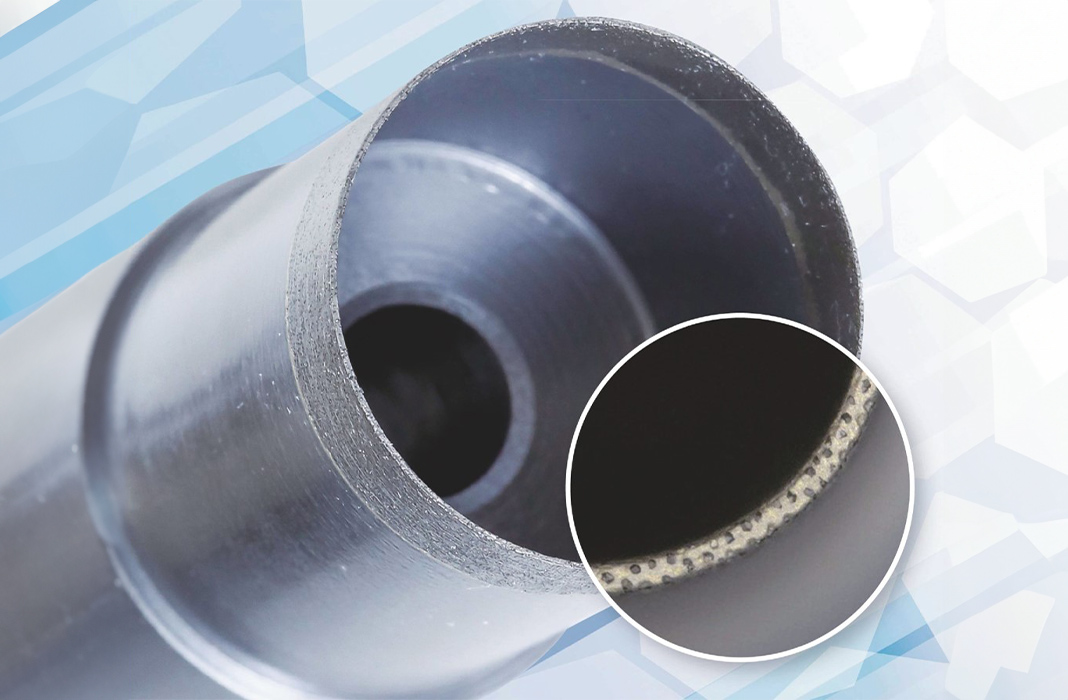
砥粒均一分散メタル砥石「ソロテル」
セラミックス素材等で生成された精密部品、機構部品の加工において、従来のメタル工具に対し、砥粒層内の砥粒を均一に分散させる技術によって、長寿命でありながら切れ味を向上させる事が可能となりました。
さらに砥粒層の超薄刃化により、硬脆性材料他、特殊材料の加工においても、加工負荷を抑えチッピングの低減など加工能率が向上し、他工具に比べて優位性を発揮します。
さらに砥粒層の超薄刃化により、硬脆性材料他、特殊材料の加工においても、加工負荷を抑えチッピングの低減など加工能率が向上し、他工具に比べて優位性を発揮します。
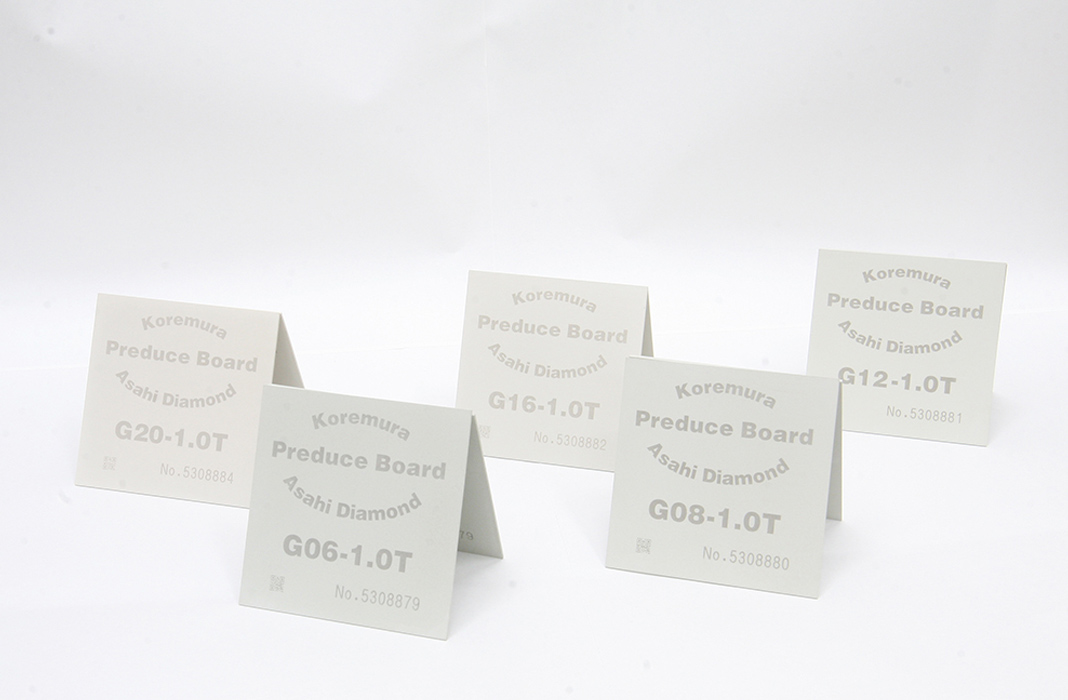
【是村旭製品】一般ドレス砥石「プリデュースボード」
一般砥粒を使用したビトリファイド砥石です。軟質から硬質まで多種な砥石組織構成が可能で、メタル工具のドレス材として効果を発揮します。
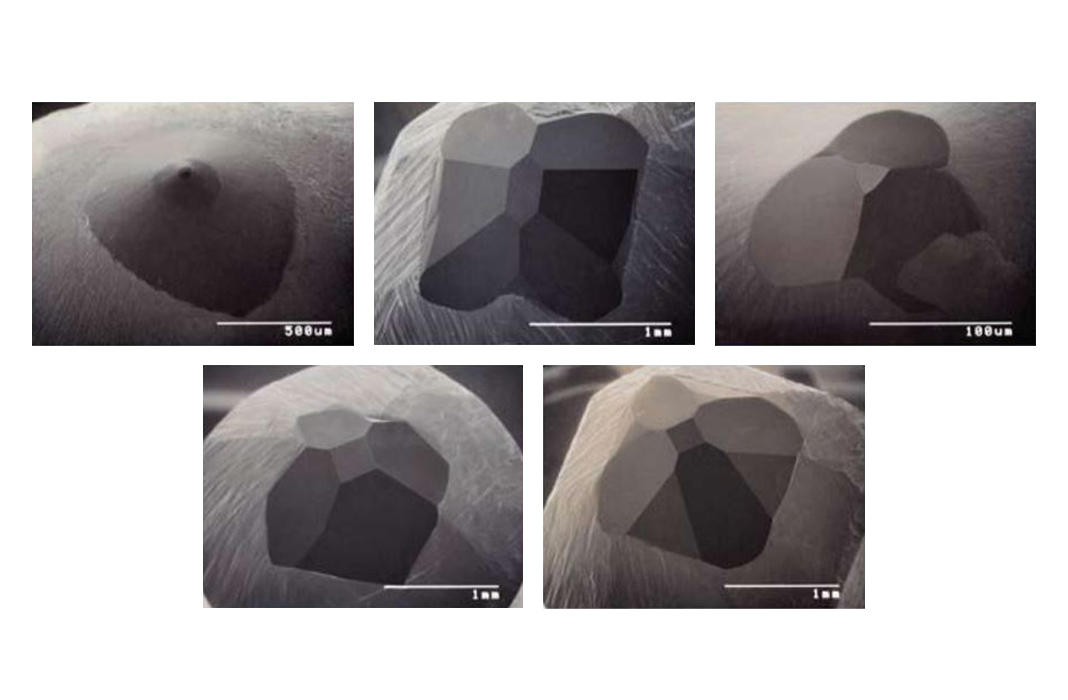
ダイヤモンドスクライバ
化合物半導体(ガリウム砒素、ガリウムリン)やサファイア等の硬脆材料の切断に使用する工具です。ダイヤモンド原石を用途に応じて円錐形状(1ポイント)や2、3、4、8ポイントの切れ刃に加工したタイプもあります。研削液を使用しないため処理施設が必要なく、スクライブラインが細いため「チップ数」が多く取れます。ブレーキング時のチッピング発生がカッタ使用時より少なく、最適な「ポイント」形状を選択できます。